Guide to choosing loading ramps
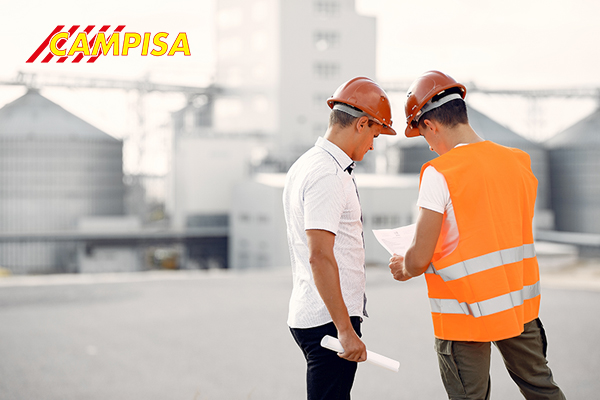
The choice of ramps is the first element to take into consideration when you want to create a loading bay for your logistics or industrial hub.
In this article, Campisa technicians provide you with some key advice, to guide you in choosing the best dock ramp.
Here you can find the main elements to be considered:
1 MODEL AND TYPE OF RAMP FOR LOADING AND UNLOADING GOODS
In its 50 years of industrial history , Campisa has developed and patented various models of loading ramps, aimed at satisfying all company needs and to match the different pit construction systems.
For this reason, the guide to choosing loading ramps starts with the model that best suits your needs. Here are the two categories of ramps and how they work:
RAMPS WITH RADIUS LIP: they are the simplest and cheapest version. It is operated with a single command which allows its lifting up to the maximum height, with the associated rotation of the spout in the extended position. When the command is released, the ramp slowly descends until it joins the vehicle floor, creating a connecting bridge between the building and the vehicle. Once the loading or unloading operation is completed, by pressing the button again, the loading ramp rises and at the same time the lip closes to return to the rest position.
LOADING RAMPS WITH TELESCOPIC LIP: compared to ramps for loading spouts with radius spouts, these are the most performing version and offer greater flexibility of use.
Pressing the start control raises the ramp to the level of the vehicle bed. Through a second “lip out” command, the lip of the platform is superimposed on the platform to form a bridge for the transit of forklift trucks.
Once the loading and unloading operations have been completed, by pressing the “lip in” button, the spout retracts completely and returns to its rest position.
The lip can have an extension of 500 mm or 1000 mm, the latter used only in special cases such as built-in bays for cold rooms.
2 LENGTH AND WIDTH OF INDUSTRIAL LOADING RAMPS
One of the fundamental elements to take into consideration when choosing the loading ramp is its length, which varies according to the height of the dock and the type of operating means used.
- Pallet truck: maximum recommended slope 4%.
- Forklifts: maximum recommended slope 8%.
Remember that the maximum slope of 12.5% foreseen by the European Standard EN 1398 is the maximum non-slip slope for people.
The height of the quay is a critical element, as it can cause accidental damage to vehicles and vehicles.
For example, if its height is lower than the vehicle, there is a high risk of impact when reversing.
To prevent the risk of accidents, Campisa has patented and developed a range of bumpers for loading docks, specially designed to adapt to the different vehicle categories:
- Semi-trailers and large trailers: a dock height of 1,200 mm is recommended. The floors that have a height between about 900 mm and 1500 mm with maximum slopes lower than the 12.5% envisaged by the EN 1398 standard can be connected with ramps 2500 mm long.
- Medium sized trailers and city vehicles: a dock height of 1,100mm is recommended.
As regards the width of the ramps, this must be as close as possible to that of the overlapping vehicle floor, up to 25 cm less than the width of the vehicle floor:
- For semi-trailers and large trailers, loading ramps 2200 mm wide, with two side flaps that automatically reduce the edge by 130-180 mm on each side, in case of connecting narrower vehicles.
- For vehicles with an external width of 2300 mm, 2000 mm wide loading ramps with two side flaps which automatically reduce the edge by 130-180 mm per side when connecting narrower vehicles.
3 CAPACITY OF THE LOADING RAMPS
The capacities are standardized in consideration of the maximum load. The EN 1398 standard provides that the loading platform capacity is calculated on a single axle of the forklift, on two wheels 1 meter apart.
Other types of calculations, such as uniform distributed load (two/three times greater than concentrated flow) are not relevant to the type of use that will occur.
The most standardized capacity is 6 concentrated tons; lower capacities mean insignificant savings. For higher capacities or faster transits (the requirement allows crossing at 5 km/h) loading ramps with a concentrated capacity of 9 tons are recommended.
4 PROJECTS FOR SPECIAL NEEDS
When ramps need to be adapted to particular situations, Campisa develops special projects to adapt to any company context. For example:
- Special loads require special loading ramps. For example, ramps up to 5 meters long to connect the 1.2 m high platform to the floors of short vehicles with a height of only 60 cm from the ground. Dock levellers of this length allow the transit of electric pallet trucks.
- For very humid environments , special hot-dip galvanized dock levellers are recommended.
- For cold rooms, the recessed platform system is recommended, in which the platform remains closed inside the building when not in use, with the sectional door closing in front. In this case the ramp is telescopic with a 1 meter protruding lip.
LOADING RAMPS: REQUEST A FREE QUOT
If you are looking for a partner to build a new logistics hub, Campisa has been a world leader in the loading bays sector for over 50 years.
We are at the service of companies to support them in choosing the best solutions for their business.
To find out the prices of loading docks and ramps , please fill in the contact box at the bottom of the page by entering your data, or you can call us via the toll-free number and schedule a consultation with one of our specialized technicians at your location.